3D Printing Technologies: A Comparison
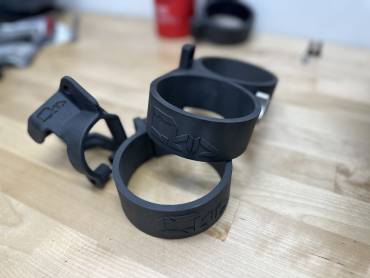
3D printing is an ever-evolving technology with diverse applications, offering a vast amount of
possibilities in various industries. To better understand its capabilities, let’s explore and compare the
four most common 3D printing technologies: Fused Deposition Modeling (FDM), Stereolithography
(SLA), Selective Laser Sintering (SLS), and Direct Metal Laser Sintering (DMLS).
Selective Laser Sintering (SLS):
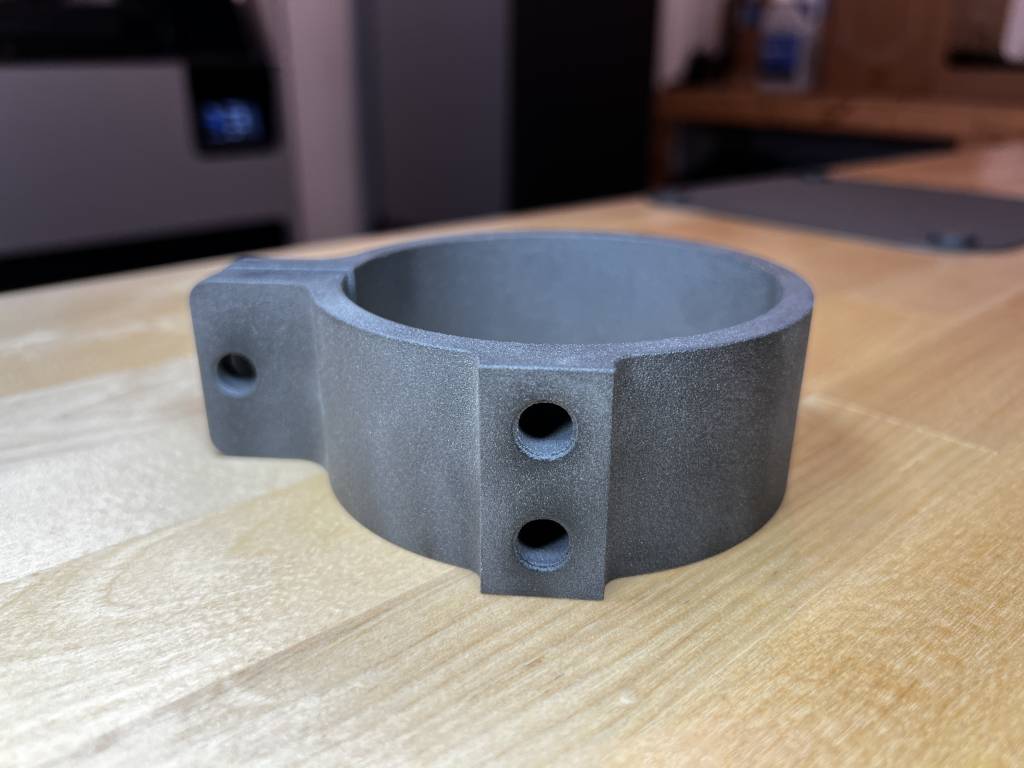
SLS uses a laser to selectively fuse powdered material, creating a solid 3D object with impressive
capabilities.
Advantages of SLS:
- Ability to create complex geometries: SLS excels at fabricating intricate and sophisticated shapes.
- High strength parts: SLS-printed objects are renowned for their durability and mechanical robustness.
- Wide range of materials: SLS supports various materials including Nylon, a highly capable thermoplastic for both functional prototyping and end-use production and TPU, an ideal material for producing flexible, skin-safe prototypes and end-use parts.
Disadvantages of SLS:
- Expensive: SLS printers can be more costly than both FDM and SLA counterparts.
Direct Metal Laser Sintering (DMLS):
DMLS utilizes a laser to melt powdered metal, selectively fusing particles together to form a solid metal
object.
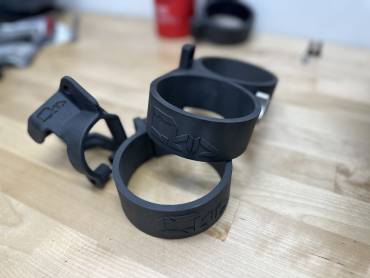
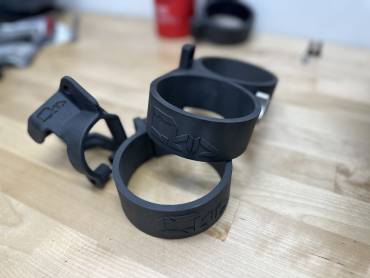
Fused Deposition Modeling (FDM):
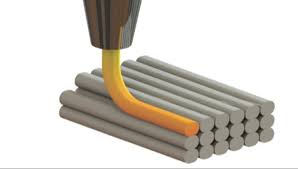
FDM stands as the most prevalent 3D printing technology today, known for its cost-effectiveness and
user-friendly nature. FDM printers use a heated nozzle to melt thermoplastic filament, which is then
carefully deposited layer by layer, shaping a three-dimensional object.
Advantages of FDM:
- Low cost: FDM printers are relatively affordable, making them accessible to a broad user base.
- Ease of use: Its simple setup and operation make FDM an attractive choice for beginners and
hobbyists. - Wide range of materials: FDM supports various thermoplastic materials, enhancing its versatility.
Disadvantages of FDM:
- Rough surface finish: FDM-printed objects may exhibit a slightly coarse texture.
- Low mechanical strength: Compared to other technologies, FDM parts might be less robust.
Stereolithography (SLA):
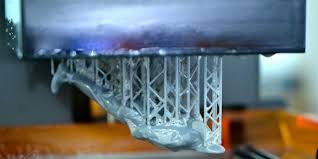
SLA utilizes a laser to solidify liquid resin, tracing each cross-section of the 3D model to create the final
object.
Advantages of SLA:
- High resolution: SLA can produce intricate details and fine features with excellent precision.
- Smooth surface finish: SLA-printed objects boast a smooth and refined appearance.
- Good mechanical strength: The strength of SLA parts is commendable, suitable for functional
prototypes.
Disadvantages of SLA:
- Expensive: SLA printers are generally more costly, which can be a deterrent for some users.
- Requires post-curing: A post-curing process is necessary to ensure the material achieves its full
properties, adding extra time to the printing process.
Advantages of DMLS:
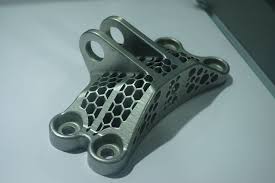
- Strong, durable metal parts: DMLS creates exceptionally sturdy and reliable metal components.
- Superior strength: DMLS-printed metal parts often surpass the mechanical properties of those
produced using other 3D printing technologies.
Disadvantages of DMLS:
- More expensive than other 3D printing technologies: The advanced nature of DMLS reflects in its
higher price point.
In conclusion, the selection of a 3D printing technology largely depends on the specific requirements of
the project. Fused Deposition Modeling (FDM) stands as a cost-effective and straightforward option,
while Stereolithography (SLA) offers high-resolution and smooth finishes. On the other hand, Selective
Laser Sintering (SLS) excels in creating complex geometries and strong parts, whereas Direct Metal Laser
Sintering (DMLS) is the go-to choice for robust metal components.
Stay informed about the advancements in 3D printing technology as the field continues to evolve,
unlocking even more possibilities for various industries and applications. If you have any questions or
need further assistance, please feel free to reach out. Happy printing!
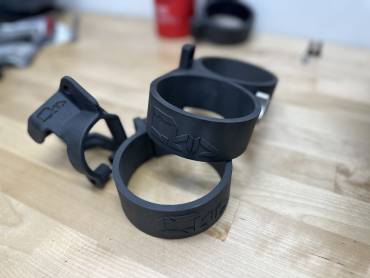